Winter Freight Shipping Risks & How to Prepare
Have you ever gone into a grocery store in the middle of winter and noticed that a lot of products are missing from the shelves? That box of cookies you wanted hasn’t been restocked, and the clerk says, “My guess is we will have it by Thursday, once this snow passes.”
Our grocery stores, our refineries, our entire economy suffers when the weather gets rough, especially during the winter season. From severe winter storms to freezing temperatures and icy roads, when roads are too dangerous to drive on, our supply chains stall, shipment delays increase, prices rise, and our lives are suddenly affected.
With the Buffalo area seeing over 6.5 feet of snowfall in just four days in late November, and areas of Washington on the east coast and Seattle out west both already experiencing supply chain disruptions caused by winter storms and snow, businesses are bracing for a hard winter season. Shippers need to plan for inevitable seasons of bad weather and rough road conditions during the winter months so that their customers don’t suffer, their supply chain keeps moving forward, and their products can be regularly delivered.
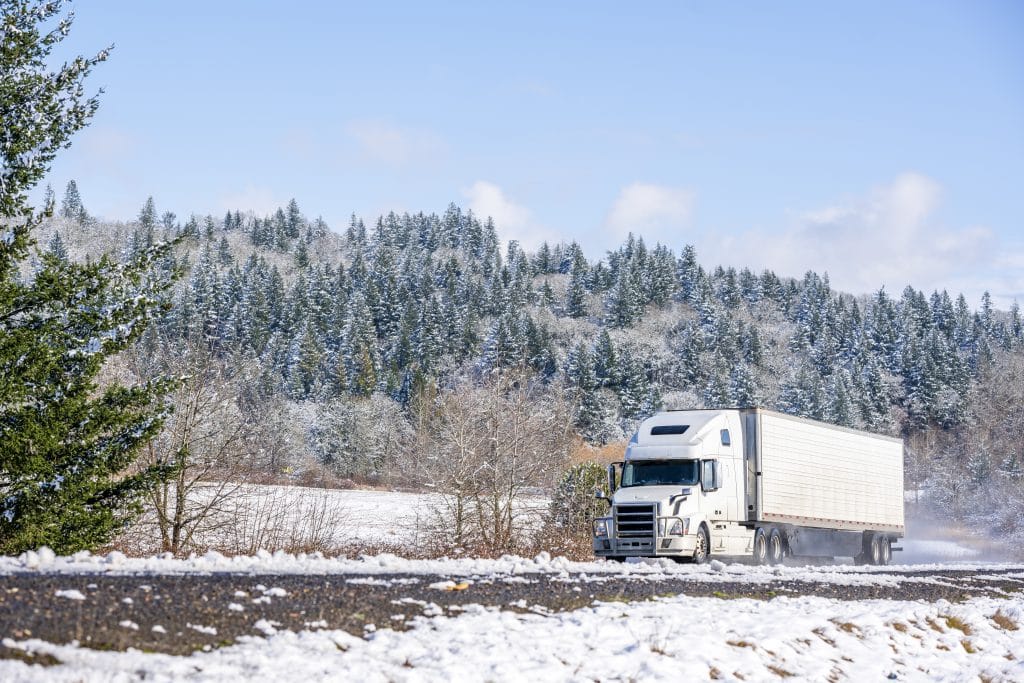
Carrier safety
First and foremost, winter weather always poses safety concerns for truck drivers. Truckers have to take a look at their lanes and determine if running a load is going to be safe in bad weather.
Veteran over-the-road drivers know that a flipped truck costs more than missing a few loads that may pay well. Even if truckers drive safely, during periods of cold winter weather there is always a chance that road conditions will be so severe that traffic gridlocks or roads close down altogether.
Nearly 12% of the total estimated truck delays are due to weather in the 20 U.S. cities with the highest volume of truck traffic. Snow and ice storms are clear culprits when it comes to winter freight shipping delays, claiming more than 544 million vehicle-hours annually.
With longer transit times during these periods of extreme cold, carriers can spend their entire HOS (hours of service) for a day slowly inching through traffic, burning through fuel and losing money.
The best way for shippers to avoid weather-related safety issues is to avoid them entirely. Of course with winter freight shipping, this can be nearly impossible. So the next best thing is to be able to constantly monitor traffic and weather conditions for each of your freight shipments.
Shipwell's holistic TMS solution integrates these capabilities into your route maps through visual overlays that work in sync with proactive issue monitoring and resolution capabilities, allowing you to avoid disruption-prone areas, avoid potential delays, suggest alternative routes, and provide accurate information to customers.
High customer expectations
Shippers failing to deliver their products results in unhappy customers awaiting pallets of food or resources. Around 70% of the U.S. population lives in snowy regions, where the same percentage of the nation's roads are also located, making efficient winter freight shipping a vital lifeline for the majority of Americans.
Having a plan of action for delivering products during poor weather conditions is crucial, even if it is just managing expectations.
Developing that plan of action with limited shipment data is a hit-or-miss operation. To enable shippers to see the negative effects of poor supply chain performance, Shipwell's data analytics go beyond the shipment itself.
With a TMS solution that provides visibility into data across departments and workflows, shippers are able to identify exactly where there is room for improvement along their supply chain and make proactive decisions with pinpoint accuracy in real-time to improve the customer experience while reducing costs, strengthening carrier relationships and boosting operational performance.
Production issues
Cold temperatures and bad winter weather pose a threat to production warehouses and terminals just as much as highways, roads and other aspects of the supply chain. When winter storms blow in, ports can shut down, intermodal networks can close, power can go out, and ships stay put until the storm passes.
Shippers end up paying more in drayage fees to get their containers out of the port. In some regions, the weather can be too harsh for warehouse workers to show up for work, limiting the amount of manpower to load a truck. Worst of all, if the power goes out at a facility, there’s not much you can do except wait for the power company to fix it.
Increasing Costs
When the weather is bad, capacity goes down. As a result, the cost of shipping in bad weather can skyrocket to make up for that limited carrier capacity, and those costs are only going up. For example, the winter storm that hit Texas in 2021 is estimated to have cost supply chains upwards of $10 billion — and that’s just for a single weather event. It is nearly impossible during the best of years to stay on budget for shipments for a myriad of reasons.
With access to an integrated network of carriers, pricing intelligence forecasting and advanced analytics, Shipwell allows you to explore the rates that each carrier is or has recently been charging for different service types and lanes. Whether you’re looking to negotiate rates with new carriers, lower the rates you’re paying to your existing partners, or just looking for more shipping options, knowing the current market rates provides a huge advantage to negotiations.
What's more, combining this premium carrier network with Shipwell's data-powered TMS allows for more strategic consolidation than manual processes allow for. With access to each shipment in your inventory and every carrier in the network, the solution can identify which shipments can be consolidated into a single load, saving costs, cutting down on capacity requirements, and reducing your carbon footprint.
Don't let winter weather hold back your supply chain
There are about 156,000 crashes annually due to icy roads in the USA. High winds, debris, blowing snow and icy roads can affect truck stability. Frigid temperatures and extreme weather conditions can close down lanes for weeks. Low temperatures can even affect vehicle performance and cargo quality.
Shipwell believes that maintaining safety throughout your supply chain is above anything else in these situations. We admire and appreciate those in the industry who risk their lives to keep our country running.
Our team wants to be a solution for your winter shipping needs by making complicated logistics intuitive and straightforward. No matter what obstacles our industry faces, we’re here to help ensure freight gets on the road as quickly and safely as possible.
Start working with us
To learn more about how Shipwell can help you to navigate the winter months and beyond to keep your shipments on track in the face of disruption — whatever the cause — schedule a demo with one of our experts today.
Get the report
Compete the form below to download your complimentary copy of "Rerouting and Resilience in the Tariff Era".