Beyond the Price Tag: Unmasking the Total Cost of Ownership for a TMS
In today's business landscape, uncovering ways to optimize transportation management is no longer a luxury — it’s absolutely essential for maintaining operational efficiency and meeting customer demands. So it makes sense that Transportation Management Systems (TMS) have emerged as vital tools for streamlining logistics and enhancing supply chain processes. It also makes sense that as companies explore TMS solutions, the focus tends to gravitate toward the initial purchase price. However, this narrow perspective can lead to overlooking the bigger financial picture.
The key to making informed decisions lies in understanding that the sticker price of a TMS is only part of the real cost involved in getting (and keeping) that TMS running. This is why it’s essential to consider the Total Cost of Ownership (TCO) associated with your chosen solution.
The costs that go into calculating the TCO of a TMS encompass all expenses associated with the solution throughout its lifecycle. This includes not only the initial purchase cost but also ongoing expenses like maintenance, support, upgrades, and unforeseen costs, and it’s only by comprehensively assessing them that businesses can make more informed financial decisions, avoiding unpleasant surprises down the road.
Wondering how to calculate it? Continue reading to find out.
Factors Contributing to TMS Total Cost of Ownership
1.
Implementation Costs
The implementation phase sets the foundation for a successful TMS integration. However, in some cases, it's also a phase that can involve its own set of costs — not the least of which can be incurred if anything goes wrong. In a survey across various industries, unplanned downtime (like that associated with disruptions during TMS implementation) costs a business $260,000 per hour on average, and that number climbs into the millions for sectors like the automotive industry. This is why it’s vital to look beyond the sticker price and thoroughly assess the true cost of implementation by factoring in:
- Software Customization and Integration Expenses: Tailoring the TMS to fit your business processes and requirements might come with additional charges. For instance, if a retail company's TMS doesn't integrate smoothly with their existing inventory management system, it could result in missed orders, inventory discrepancies, and ultimately, customer dissatisfaction.
- Training and Onboarding: Properly trained employees are key to maximizing the benefits of your TMS. Investing in comprehensive training prevents costly errors. For instance, a manufacturing company that fails to adequately train its workforce on the new TMS might experience production line disruptions, leading to delays and lost revenue.
- Data Migration and Setup: Neglecting data migration can lead to inaccuracies, double entries, and data loss. Imagine an e-commerce business without proper data migration during TMS implementation; they could face inventory discrepancies, inaccurate customer orders, and potential legal implications due to mishandled customer data.
- Disruption to Regular Operations: Implementing a TMS can cause temporary disruptions. If not planned for, these disruptions could lead to decreased productivity and revenue loss. For example, a shipping company undergoing TMS implementation during the holiday season might experience shipping delays and customer dissatisfaction due to disruptions in their usual processes.
2.
Maintenance and Support Costs
After the implementation of your new solution, ensuring you are able to continue to benefit from ongoing maintenance and support is vital to the sustained success of the TMS. And yet despite this, many companies tend to underestimate the costs involved in ensuring this happens, leading to unexpected financial strain over time as a result of long-term negative impacts such as:
- Regular Software Updates: Failing to stay updated with the latest software versions might result in security vulnerabilities, system inefficiencies, and potential data breaches. For instance, not updating a TMS with security patches could expose sensitive customer information, resulting in regulatory fines and reputational damage.
- Technical Support and Troubleshooting: Without a reliable technical support plan, resolving issues can be time-consuming and costly. Consider a scenario where a logistics company experiences a critical system glitch during peak shipping season. Without immediate technical support, the delays could lead to missed deadlines, customer complaints, and lost business opportunities.
- Infrastructure Maintenance: On-premises TMS solutions require hardware maintenance and upgrades. Neglecting this aspect could lead to system failures, downtime, and loss of revenue. A distribution center without proactive server maintenance might experience a sudden hardware failure, causing shipment tracking delays and customer dissatisfaction.
- Downtime Consideration: Not factoring in potential downtime can have direct financial consequences. A manufacturing company facing unexpected downtime due to TMS maintenance might experience a halt in production, leading to missed delivery deadlines and contractual penalties.
3.
Hidden Fees and Unforeseen Costs
Unanticipated costs can arise if hidden fees are not accounted for during TMS evaluation — and with many providers, they’re surprisingly common. Things like requiring licensing for a new WMS service alone can add an average of $1,500 per month to previously anticipated costs, along with other issues that can impact your initial budget projections through unplanned expenses like:
- Third-Party Integration Charges: Integrating the TMS with third-party services might lead to additional expenses. A logistics company integrating the TMS with a new GPS tracking system might face unexpected integration costs that strain their budget.
- Licensing Fees for Additional Features: As your business needs evolve, additional features may become necessary. Not budgeting for these features could hinder operational efficiency. For instance, an e-commerce business that experiences growth might require additional warehouse management capabilities, incurring unforeseen licensing fees if those capabilities were not included in the initial solution.
- Scaling Costs: If your business experiences growth, scaling the TMS might lead to unplanned expenditures. A transportation company unprepared for sudden growth might need to upgrade their TMS to handle the increased load, incurring additional costs for licenses, hardware, and implementation.
- Penalties and Contract Breaches: Not adhering to contract terms can result in financial penalties. Consider a scenario where a retail company decides to terminate the TMS contract prematurely. The resulting penalties could be substantial and impact the company's bottom line.
How to Evaluate the TCO of a TMS
Assessing the total cost of ownership for a Transportation Management System (TMS) might seem like a challenging task, but as highlighted above — it's a crucial one. By breaking down the evaluation process into manageable steps, you'll be able to gain a clearer understanding of the comprehensive financial impact of your TMS investment over time. Below, we outline the steps to take in order to simplify this process, enabling you to comprehensively assess the long-term financial impact of your TMS investment.
1.
Conduct a Thorough Evaluation
When selecting a TMS vendor, ensure you're making an informed decision and won’t be caught off guard by:
- Researching Vendor Reputation: Investigate the vendor's track record, customer feedback, and history of pricing changes.
- Requesting a Detailed Cost Breakdown: Ask for a comprehensive breakdown of all costs, including any potential hidden fees.
- Seeking out Client References: Reach out to current clients to gain insights into their experiences with the vendor's pricing structure and transparency.
2.
Establish a Detailed Cost Projection
Create a thorough cost projection analysis to anticipate future financial commitments by:
- Creating a Comprehensive Spreadsheet: Develop a detailed spreadsheet to track all potential costs, ensuring nothing is overlooked.
- Analyzing One-Time vs. Recurring Costs: Differentiate between one-time expenses and recurring fees for more accurate calculations.
- Establishing a Long-Term Estimate: Estimate costs over a specific time horizon (3, 5, or 10 years), factoring in potential business growth and evolving needs.
3.
Consider the Long-Term ROI and Value
To determine the true value of the TMS investment, consider both costs and benefits over the long term by:
- Analyzing Anticipated Benefits: Assess the expected benefits and potential cost savings the TMS will bring to your operations.
- Weighing Long-Term Value: Compare the long-term value the TMS provides against the overall costs.
- Calculating Breakeven Point: Determine when the accumulated benefits surpass the total costs, leading to a positive ROI.
For more information on how to weigh all of these factors and come to a realistic evaluation as to what your chosen TMS solution will be capable of delivering in the long term, get a complete breakdown in our step-by-step guide.
DOWNLOAD THE GUIDE!
What’s Next?
In the world of TMS solutions, it's easy to get fixated on the initial purchase price — something that many vendors love to take advantage of that fact through promises of low-cost or even “free” TMS solutions. However, to make truly informed decisions, businesses must remember, it's not just about the price tag, it's about the value the TMS brings and the financial health of your organization in the long run. Armed with this knowledge, readers can confidently navigate the TMS landscape and make strategic choices that ensure that they aren’t caught off guard, and are able to enjoy lasting benefits from their chosen TMS solution well into the future.
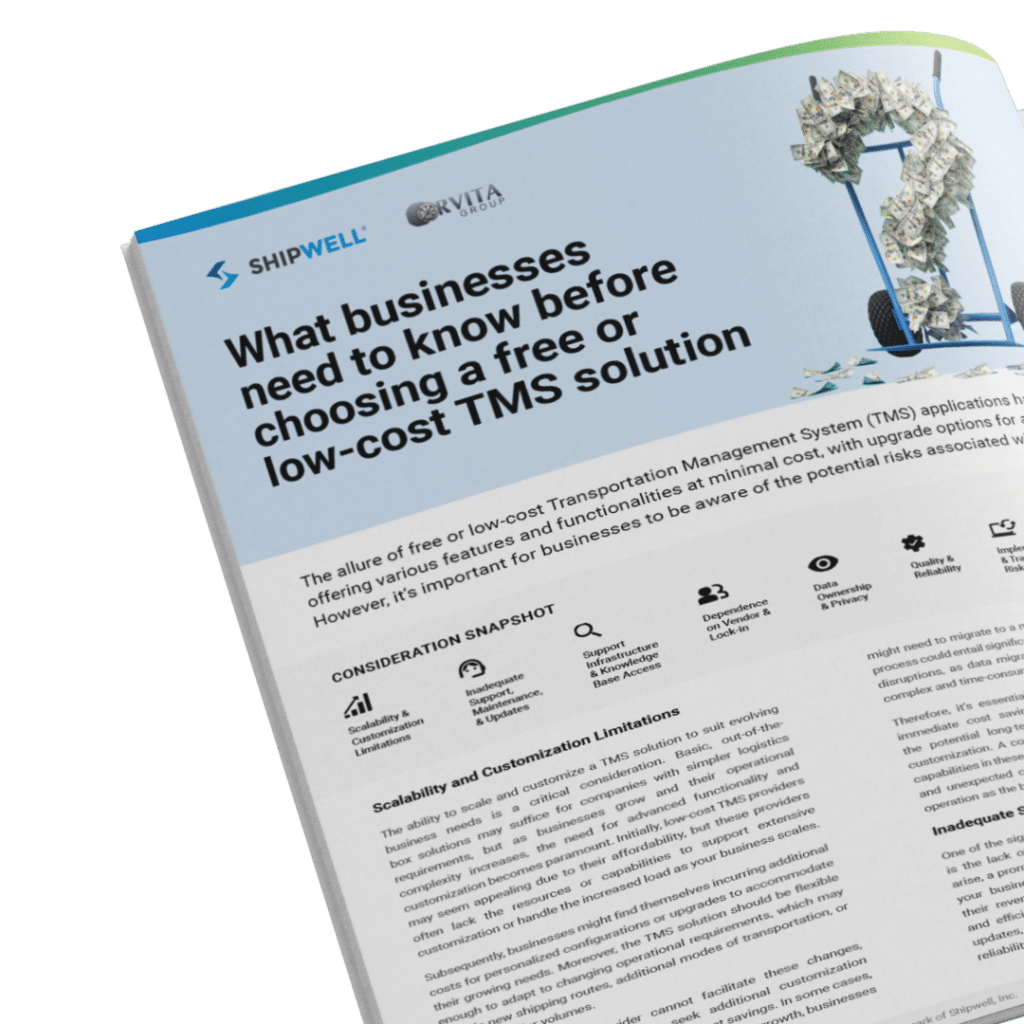
Looking for More?
For more information on how to assess the risks associated with placing “purchase price” above the total cost of ownership in your hunt for your ideal TMS solution, download our detailed guide on what to consider — and make the most informed decision for your business.
Get the report
Compete the form below to download your complimentary copy of "Rerouting and Resilience in the Tariff Era".