Why Visibility Matters During Produce Season
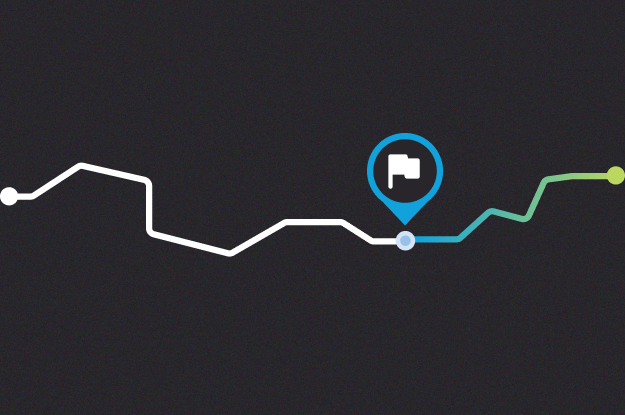
As temperatures continue to rise throughout late winter and into spring, produce season kicks into full gear across the country and continues well through the summer months. During this time produce shippers face quick turnarounds and high demand, but meeting expectations for timely deliveries in the race to get crops out of the fields and onto store shelves can be a challenge even during the best of times — and these are not the best of times for supply chains.
Because of the short timeframes involved in ensuring that shipments arrive fresh, the produce supply chain is one of the most fast-paced there is, and the amount of effort that goes into ensuring that deadlines are met takes significant effort and coordination. If a shipment arrives late for its scheduled pickup or delivery, it can easily result in as much as a day or more of freshness lost. And with customer expectations around the quality and freshness of the food they buy being higher than ever, that can have a negative impact on customer satisfaction that goes far beyond the effect that late shipments can have on other products.
In order to meet consumer expectations and ensure that produce and other cold chain logistic shipments adhere to their timelines in the face of a shortage of over 80,000 drivers, rising wait times at loading docks, the increasing impact of climate change, and other issues affecting supply chains across the country, you need visibility that goes beyond the standard track and trace capabilities that are commonly employed in shipping solutions.
For example, delays at loading docks commonly occur when the shipper or receiver changes or miscalculates the scheduled appointment time. In order to avoid this, shippers should look for the best transportation management system that provides accurate, real-time ETAs that go beyond standard point-in-time location, factoring in all the complex variables that can impact arrival times, like weather and traffic conditions. By having access to accurate information on when a cold chain transport will arrive at its destination, schedules can be adjusted and communicated well in advance, giving receivers the opportunity to adapt and prepare for quicker loading or unloading.
Likewise, when it comes to managing issues that arise while a shipment is enroute, having visibility to look into what’s causing them and how to resolve them — or even better, recognizing them in advance so you can get ahead of them — can help immensely. Getting a clear view into what loads are not being tracked, where shipments are overdue or running late and other common issues takes valuable time out of a supply chain manager’s day. And while existing solutions may be capable of providing visibility into those issues, it’s typically up to the individual user to identify them. So by taking visibility further through instant access to real-time data paired with AI and machine learning to drill into the details, TMS shippers can be able to find out where there are hold-ups, quality issues, or waste in the supply chain.
Once these issues are known, the same AI and machine learning tools can be leveraged to determine the best method for addressing them. Currently, even when the solution is clear, contacting carriers, rescheduling shipments, updating information, or otherwise implementing a solution typically means navigating to different systems or screens where human error can enter the equation. However, by bringing actionable solutions to the same centralized dashboard housing all the detected issues across the supply chain, it becomes possible to not only view where exceptions have occurred, but correct them instantly.
How does Shipwell improve supply chain visibility?
Keeping shipments on track for on-time pickups and deliveries is a vital part of every industry, and even more so for those that deal with fresh produce shipments. Without visibility into what’s happening across the entire supply chain and the capability to analyze the data collected to turn it into actionable solutions, even small issues can quickly turn into delays that can seriously impact both the customer experience and a business’s bottom line. To address the problems that shippers face, Shipwell’s TMS platform provides companies with an unparalleled level of visibility that delivers the insights and control needed to successfully navigate the produce season rush.
Access our connected network for full end-to-end visibility
Shipwell’s connected network offers two million ELD-connected units in its carrier network, including access to both capacity and live tracking that covers 96% of driving distance across modes of transportation like drayage, LTL, parcel and final mile.
Quickly spot and correct issues with proactive exception management
Continuously monitor all shipments throughout the shipment lifecycle from a central location, like Compass Dashboard. By proactively identifying issues and providing guided actions to address them instantly through machine learning and AI, shippers can see a 98% on-time delivery and pickup rate.
Adapt to changes in real-time with Responsive ETAs
Provides Shipwell TMS shippers with at-a-glance status updates for estimated arrival times for shipments en route, taking into account real-time freight traffic and weather conditions, along with other factors that can cause delays. Logistics managers can now see which shipments are on time, which are running late, and which are at risk of missing their scheduled delivery time, all directly on the Shipwell Platform.
Enable continuous optimization with powerful analytics and reporting
Shipwell’s data-enabled TMS solution provides both you and your customers with the information you need to take your business and shipments to the next level. View detailed reports on over 250 touchpoints including monthly spend, carrier cost, cost per mile, and more to develop a more competitive and timely strategy.
For anyone looking to move shipments during produce season, the benefits of taking steps to improve supply chain visibility are many. Not only can you more rapidly identify and address potential issues to keep shipments on track, but you can also leverage the data that comes from greater visibility to establish an effective strategy for future shipments to stay ahead of the competition. No matter how you look at it, with better transportation management and visibility through a TMS, supply chain operations receives the advantage needed to deliver consistent and reliable results in today’s environment.To learn more about how Shipwell’s advanced visibility capabilities management software can help you serve up cold chain shipping success this produce season, schedule a demo today.